Reduce, Reuse, Recycle and Redesign
With some 10,000 products available to more than 30,000 global customers in a broad range of industries, Dow Corning understands the strategic significance of providing the most current information to employees and customers — whenever and wherever needed. To help manage this mission-critical responsibility, Dow Corning turned to F.P. Horak and MarcomCentral®, from PTI Marketing Technologies™. The end result was a 25 percent reduction in fulfillment expenditures, a 20 percent reduction in printing costs, fewer back-orders, and a greater employee productivity.
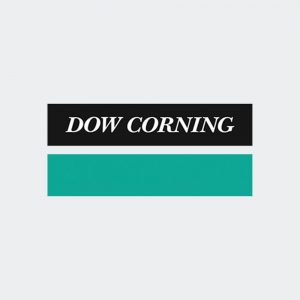
Dow Corning places great value on being responsive to customers and making it easier for customers to get the information they need the first time
The challenge
Product data sheets are updated regularly, but while the document content does change, the overall appearance of the sheet does not, making it difficult to tell which is the latest version. In addition to the thousands of ever-changing data sheets, the company produces another 2,000 corporate and marketing communications items such as brochures, stationery, and business cards. Sales representatives, customer service staff, and employees in general place more than 8,000 orders for these documents every month, resulting in monthly shipments of 100,000
pieces worldwide.
Despite having a Documentum document management system, which provides a robust digital file repository, Dow Corning found that it had far too many printed documents — many of them outdated — sitting in its warehouses. The company also realized that different versions of documents resided in different systems, including fulfillment houses, the Documentum system, fax services, and the corporate website. It was all too easy for sales and customer service representatives to inadvertently provide outdated or incorrect information, especially considering that half of Dow Corning’s employees and customers speak English as a second language. Because of the inconsistency in information, the company was also concerned with potential liability.
Why they chose MarcomCentral
Dow Corning recognized that an enterprise-wide solution was the only way to solve the problem. They started with a vision of a global printing process that would link all company warehouses together into one supply chain by initiating a single-source printing agreement with the F.P. Horak Company, a commercial printer with international partners. However, the new relationship entailed much more than printing; it was a business solution for a comprehensive warehousing, tracking, inventory reporting, and distribution system. Because Dow Corning wanted the global solution to incorporate the company’s existing document management system, a key component of F.P. Horak’s solution was MarcomCentral.
MarcomCentral and F.P. Horak offered an integrated, end-to-end enterprise solution that could adapt to Dow Corning’s future needs and would support the multiple warehousing and print options required for successful implementation. At Dow Corning, the eCatalog ensures that each order is routed to the most appropriate location throughout the world and that only the latest version of each document ordered is used in the correct language.
With some 10,000 products available to more than 30,000 global customers in a broad range of industries, Dow Corning understands the strategic significance of providing the most current information to employees and customers — whenever and wherever needed. To help manage this mission-critical responsibility, Dow Corning turned to F.P. Horak and MarcomCentral. The end result was a 25 percent reduction in fulfillment expenditures, a 20 percent reduction in printing costs, fewer back-orders, greater employee productivity, and an assurance that customers receive the right information at the right time.
The results speak for themselves
The results measured by Dow Corning include a 25 percent reduction in print-on-demand and fulfillment expenditures. An additional 20 percent reduction in printing costs came from moving to F.P Horak as a single-source print supplier and the adoption of just-in-time and print-on-demand processes. Moreover, because inventory tracking is built into the system, document owners have more real-time information for making faster decisions on print orders. This has resulted in an unexpected 50 percent reduction in literature items going to back-order status. One of the greatest values, however, is the company’s enhanced responsiveness to customer needs and getting the latest information to those who need it in the format desired.
Highlights
- 25% Less Fulfillment Cost
- 20% Fewer Printing Costs
- 50% Fewer Back Orders
- 70% Less Inventory
- Accurate Product Information
- Faster Product Information to Market
- Enhanced Responsiveness to Customer Needs
- Greater Employee Productivity
- Simplified Workflows
- Tightened Document Security
- Print Supply Chain Management
- Support of Internal eProcurement
- Improved Document Management
- Elimination of Information Obsolescence for Multiple Languages
- Marketing Branding Control